*Introduction
Electric discharge machining process : Whenever sparking takes place between two electrical contacts a small amount of material is removed from each of the contact.
This fact to used to produce sparks between the tool and work piece in EDM. It is also known as spark erosion, electro erosion of Spark machining.
Explain the working principle of Electric discharge machining process?
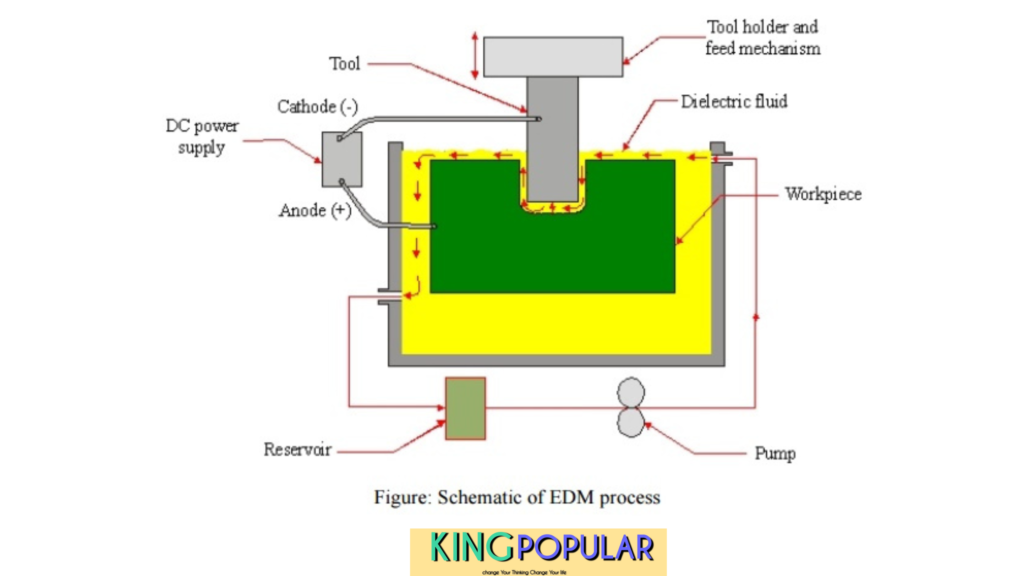
1) EDM works on the principle that heat energy generated by a Spark is used to remove material from the work piece.
2) In this Process an electric Spark gap is generated to machine the workpiece to Produce the desired shape.
3) The tool and work piece are separated by a small gap called as spark gap. The gap varies from 0.01mm to 0.5 mm. The Tool and work piece both are immersed in the dielectric fluid.
4) when supply is made ‘ON’ thousands of sparks are produced per second. The duration of each spark is short.
5) When Spark Comes in contact with the dielectric fluid in spark gap. The fluid gets ionized. The allows current to flow between the tool and work piece as shown in fig .
6) A Very high temperature of around 10000°c is generated in the spark region . As a result, the material gets melted and is removed from the workpiece.
7) The melted are Particles of the metal are then driven away by the dielectric fluid.
8) A set-up for EDM is shown in fig.
Functions of Dielectric fluid
A dielectric field should posses the following functions :-
1) It should act as insulator until the required breakdown voltage is attained.
2) It Should act as a conductor, once the break down Voltage is reached .
3) It should be clean spark gap by carrying the molten metal.
4) It should delonize the spark gap rapidly after the discharge has Occurred.
5) It should cool the tool, work piece and the spark region.
* Advantages of EDM
The advantage of EDM process are listed below:
1) Any material can be machined irrespective of its hardness .
2) Any complicated shape can produce on the workpiece.
3) There is no physical contact between the tool and the work piece. Therefore no Stresses are produced in the workpiece.
4) Delicate work piece (small electronic Parts) which can not withstand cutting force can be machined.
5) very fine holes con be easily drilled.
6) A good surface finish can be obtain.
Disadvantages of EDM
The disadvantage of EDM process are listed below:
1) Taper holes are produced.
2) Metal removal rate is low.
3) Overcut is formed.
4) can not very sharp corners.
5) Excessive tool wear occurs during machining.
6) Power consumption is high.
7) Unable to machine electrically non- conductive material.
Applications of EDM
1) It is used in making stamping tools, wire drawing and extrusion dies, header dies, forging dies etc.
2) Internal threads can be produced in harder material by using a rotary spindle.
3) In machining delicate work piece like Copper Parts are used for fiting in vaccum tubes.
4) For machining of exotic materials used in aerospace Industries.
5) In resharpening of cutting tools and broaches.
6) In Micro hole drilling, curve hole drilling.